In the field of intelligent manufacturing, the difference of a millimeter often determines the success or failure of a product. FGU07-100S Capacitive Label Sensor launched by Fuwei Electronics, with 0.2mm positioning accuracy and 5KHz high-speed response of the two core technology breakthroughs, completely subvert the accuracy and efficiency of the traditional label detection bottleneck, for automotive, electronics, pharmaceutical and other industries to provide a “zero-error” intelligent detection solutions.
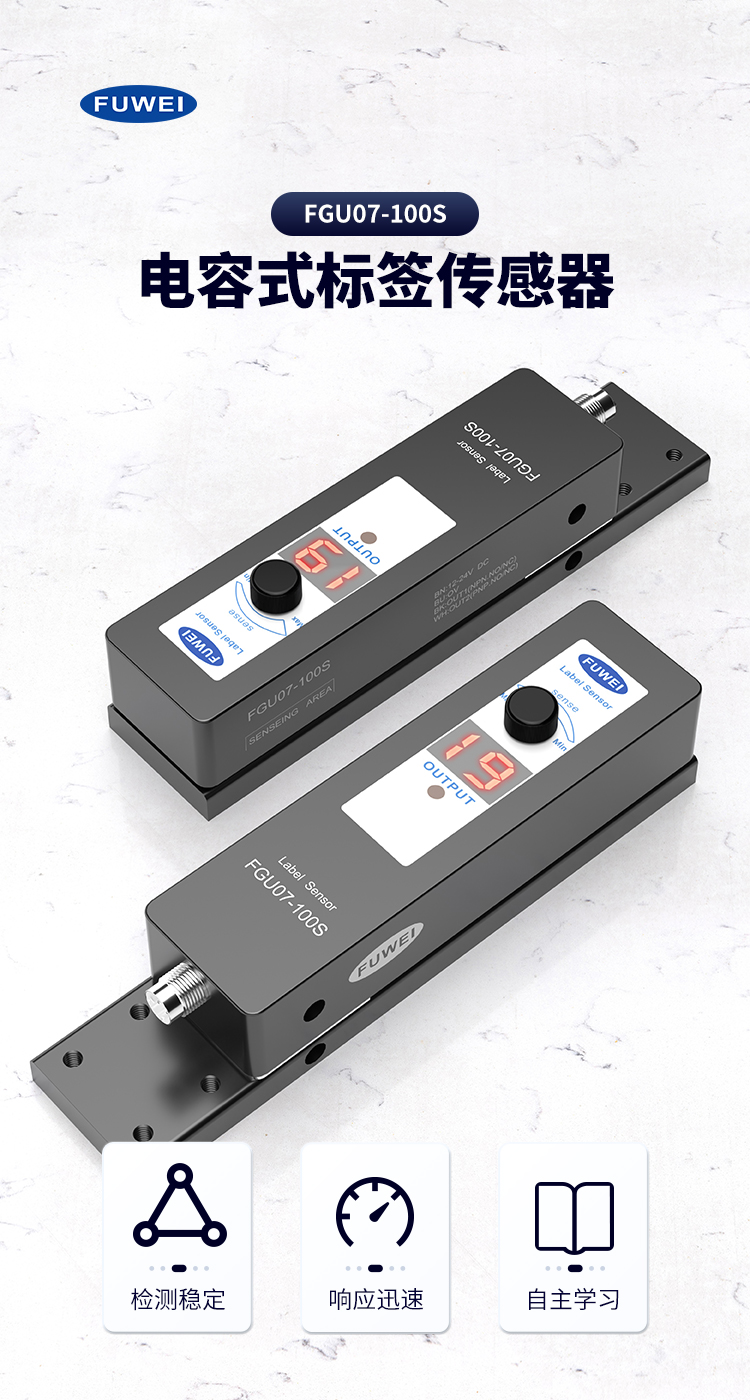
First, the traditional detection technology “millimeter trap”
Traditional photoelectric sensors rely on reflected light intensity to determine the location of the label, in the curved surface, transparent material or complex background, the detection accuracy is generally between 0.5-1mm. Data from an automotive wiring harness factory shows that the label offset error caused by manual calibration is as high as 1.2mm, which directly triggers a 0.8% product rework rate. FGU07-100S breaks through the physical limitations by capacitive sensing + dynamic compensation algorithm, realizing 0.2mm level positioning, equivalent to 1/50 of the diameter of a hair.
Second, technology decryption: 0.2mm behind the three major innovations
1. Capacitive sensing: “see-through eye” that penetrates the material.
Different from traditional photoelectric technology, FGU07-100S adopts capacitive sensing principle to recognize the label boundary by detecting the change of dielectric constant of the object. Even in the face of metal foil, PET transparent film and other complex materials, it can still accurately capture the edge of the label, solving the problem of photoelectric sensors “seeing through the light”. 
2. Dynamic compensation algorithm: adaptive to environmental interference
Equipped with AI anti-interference algorithm, the sensor can real-time compensation for temperature, humidity, vibration and other environmental variables. In the extreme temperature change test (-20℃~60℃) of a new energy battery factory, FGU07-100S still maintains a stable accuracy of ±0.2mm, while the error fluctuation of traditional sensors reaches ±0.8mm.
3. High-speed signal processing: 0.02 seconds to complete a test
Adopting a high-speed ADC analog-to-digital converter chip and a dedicated digital signal processor, FGU07-100S realizes a switching frequency of 5KHz and a response time of 20μs, which enables it to complete dynamic detection on a high-speed production line of 200m/min. A food packaging enterprise test shows that its detection speed is 20 times faster than manual, and the accuracy rate from 97% to 99.99%.
Third, the industry benchmark case: from theory to practice of cost reduction and efficiency gains
Case 1: Automobile parts factory -- accuracy increased 5 times, annual savings of 500,000 yuan
After the introduction of FGU07-100S to an automotive engine parts manufacturer, the labeling accuracy was improved from ±1.5mm to ±0.3mm, and the misdiagnosis rate dropped by 98%. The number of assembly line stoppages due to label offset dropped from 20 to 0 per month, saving over 500,000 RMB per year.
Case 2: 3C electronics factory -- micro-label inspection “breakers”.
For the 0.5mm ultra-small labels on the pole pieces of cell phone batteries, FGU07-100S realizes 100% recognition rate through ultra-micro-pitch detection technology. The data of an electronic factory shows that its detection efficiency is 3 times higher than the traditional program, and the defective rate of the product is reduced from 0.3% to 0.01%.
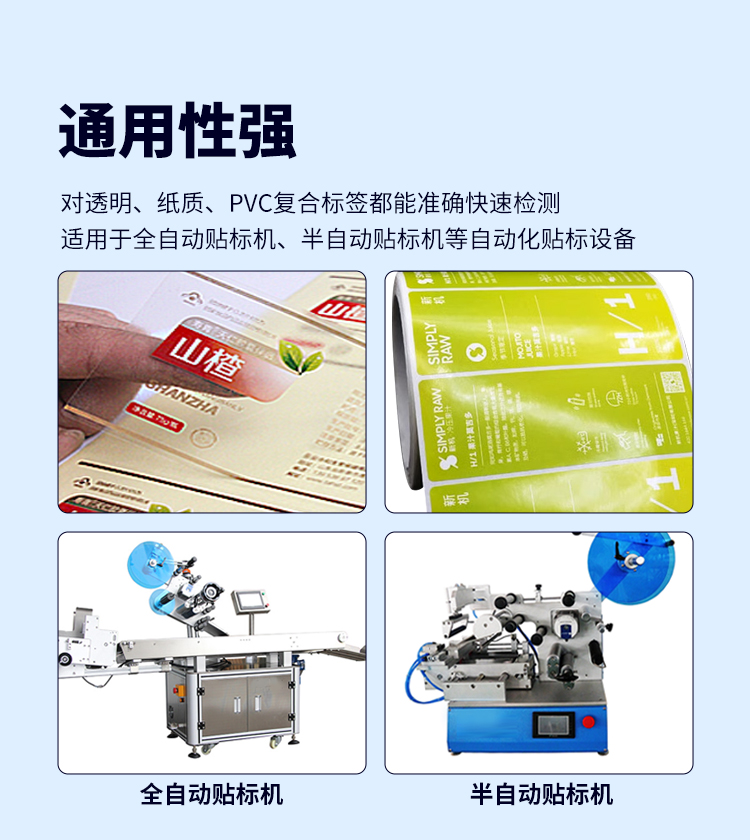
Embrace the new era of inspection technology by choosing FGU07-100S.
FGU07-100S capacitive label sensor is not only a device, but also a milestone of industrial detection accuracy. With full-stack self-research technology and scenario-based solutions, FGU07-100S helps enterprises break through the production bottleneck of “millimeter-level error” and realize the leap from “qualified manufacturing” to “precision manufacturing”. The company has been able to realize the leap from “qualified manufacturing” to “precision manufacturing”.